DANFOSS MOTOR HOW TO IMPROVE SPACE SHUTTLE MAIN MOTOR IN DELHI
Danfoss Motor Description: The Space Shuttle Main motor (SSME) program is currently utilizing the state of the motor structure known as Phase I to ensure that the space shuttle launches at 100% and 104% of rated thrust. As of May 1985, extensive ground development and qualification tests have been carried out, and 51 primary motors have been successfully launched in 17 flights. The 104% thrust and the motor life of 15 flights under this thrust meet the current launch requirements. The life of the two high-pressure turbo pumps is limited and needs to be replaced every six flights. Future launch requirements require a 109% rated thrust (vacuum thrust of 512,300 lbs) and a longer life turbo pump to minimize launch costs. Phase II of the SSME program is a high-pressure fuel and oxidant turbopump that has been developed and certified to ensure 10 flights at 109% thrust. The design changes made to the turbo pump are primarily to enable the rotating machinery to withstand the environment created by the Phase II motor design, such as turbine temperature, propellant flow, system pressure drop, asymmetric lateral force distribution, and the like. Improving the turbine's operating environment and increasing performance margins are two additional phases. The first additional phase, called Phase II+, will also incorporate design improvements to improve SSME's gas system operating environment. The main purpose of Phase II+ is to implement a two-tube gas aggregator. This new aggregator will greatly improve the characteristics of the gas stream, which flows from the high-pressure fuel turbine primary wheel outlet, through the turbine outlet header collector, the gas collector pipe to the main injector flow manifold. The main injector oxidant hollow column itself is bypassed. The reduction in pressure drop and dynamic pressure oscillations will result in a reduction in turbine operating temperature and periodic stress throughout the gas flow system. These design improvements will be validated with a large number of test instruments in conjunction with motor development tests. Flight identification will be carried out later. The second additional phase is called the Process Testbed Predecessor Program (hereafter referred to as the Predecessor), which is a process plan to verify the feasibility of the improvement. Verification by hot test can show that these changes will improve the performance and working environment of the motor. The program includes analysis, component design and production technology research, laboratory testing and verification of motor hot test runs. The overall goal of the Phase II+ program is to provide SSME with a two-tube gas aggregator and an improved pre-chamber oxidant hollow column. The goal is to improve the working environment of the motor's turbopump and to enable the motor in the sub-structured state to guarantee more than 10 flights at 109% of rated thrust. https://www.xjetl.com
4.00/5
1 reviews

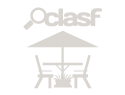

Price:
₹ 0,00
₹ 0,00
Contact
CONTACT